Our Brass Component Manufacturing Process
At Rajan Products, we are committed to delivering high-quality brass components. Our comprehensive manufacturing process ensures that each part meets your exact specifications and offers superior performance. Here's a detailed look at the steps involved.
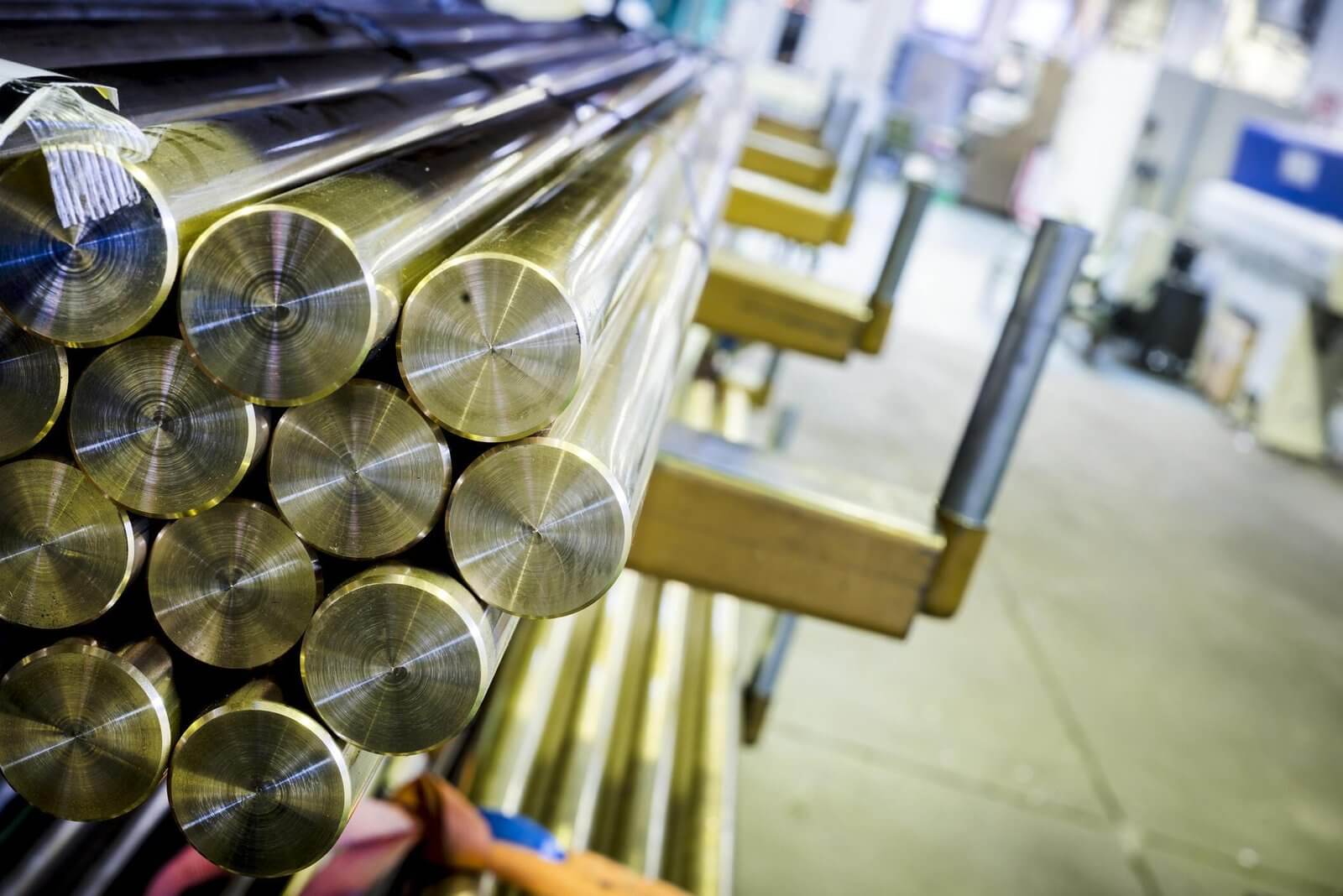
01
01.Incoming Material Inspection
- We source brass rods from reputable suppliers
- Upon arrival, each rod undergoes a meticulous inspection using micrometers to verify dimensional accuracy against your requirements.
- The raw material is then analyzed by our in-house spectrometer to confirm its chemical composition meets the designated standards.
02.Machining or Hot Forging
- Depending on the specific component design, the brass rod will be directed to either the machining department or the hot forging department.
02
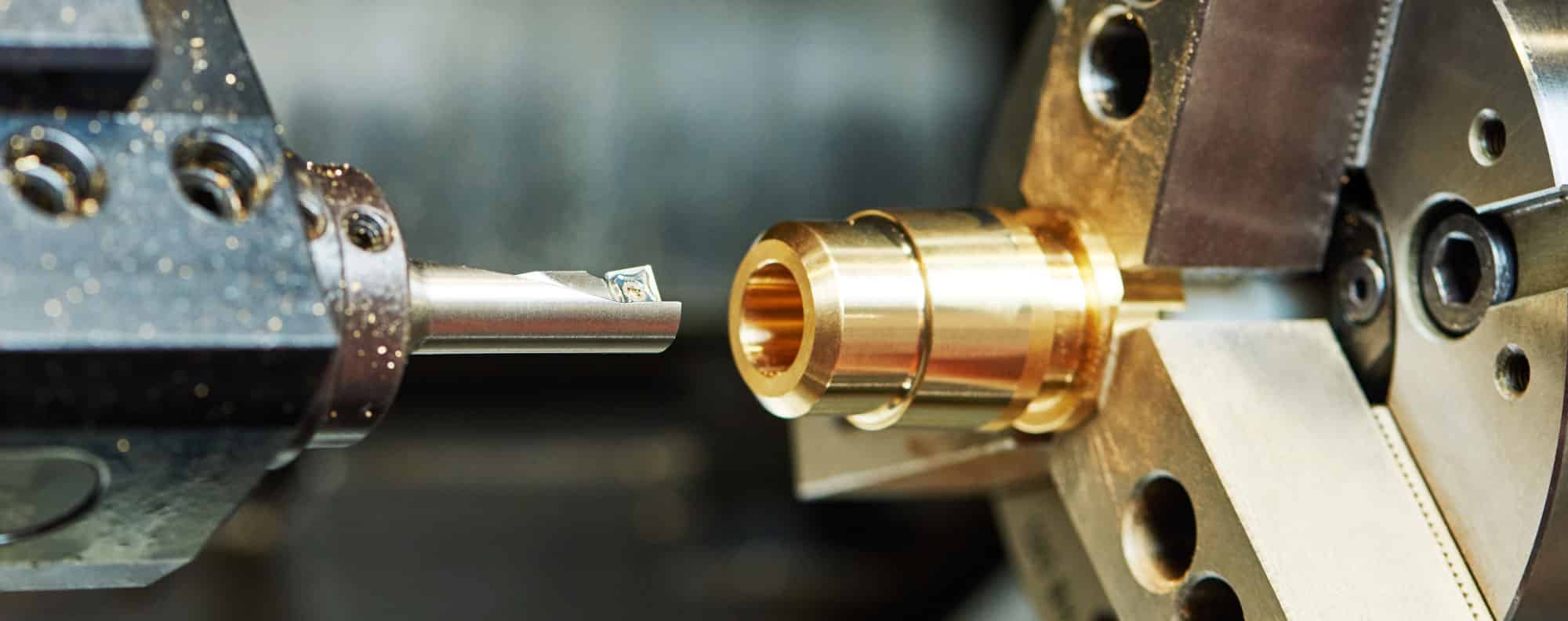
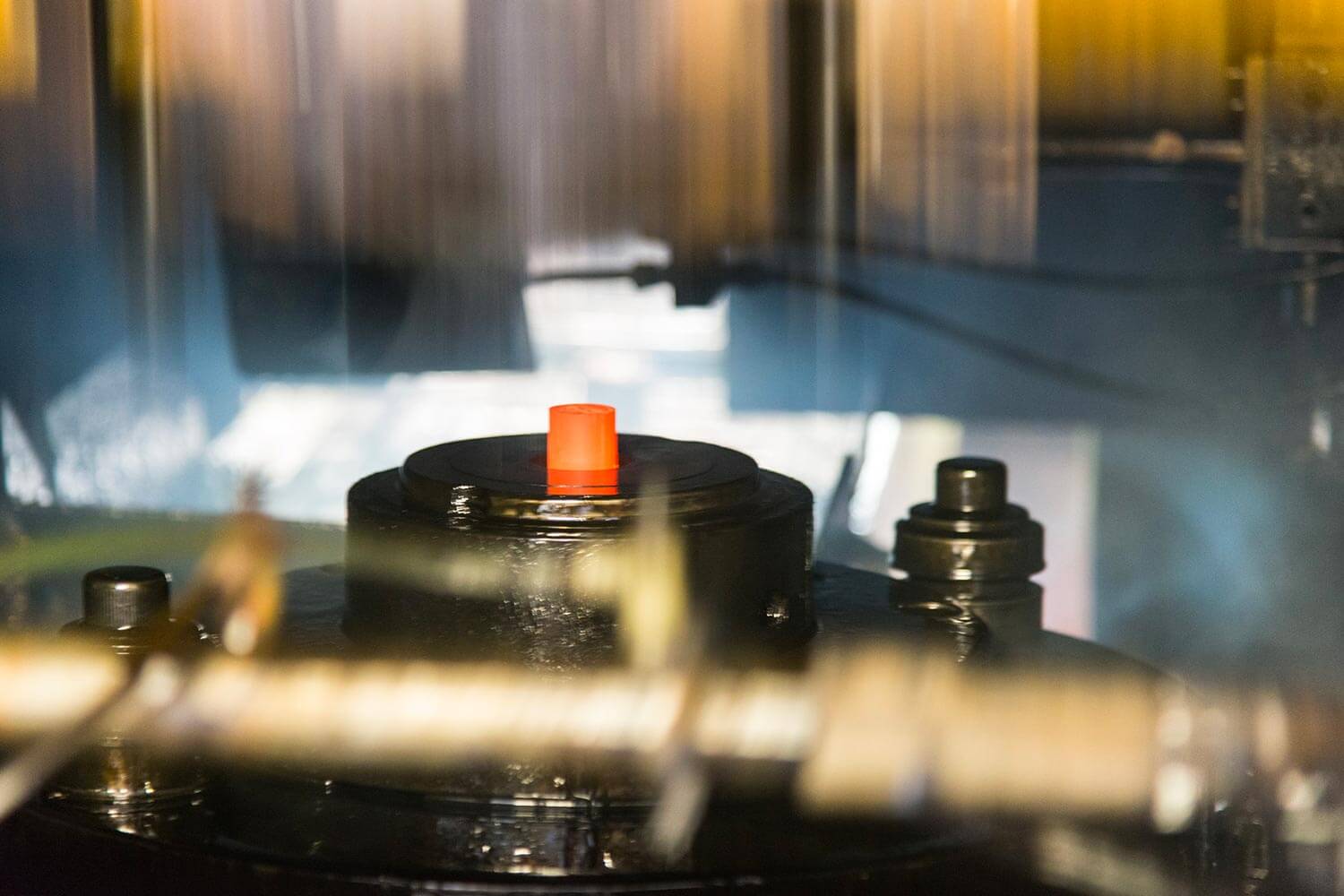
03
03.Hot Forging (if applicable)
- For components requiring hot forging, the brass rod is cut to the precise lengths needed.
- The billets are then heated to a predetermined temperature in a controlled furnace.
- The preheated billets are shaped using specialized forging equipment to achieve the desired form.
- Finally, a trimming process removes any excess material from the forged component.
- Every forged part undergoes a rigorous inspection to ensure dimensional accuracy and identify any potential cracks.
04.Machining
- Brass rods or pre-forged components are then machined to achieve the final dimensions as per your specifications.
- This department utilizes various techniques such as drilling, milling, turning, and tapping to create the intricate features of the parts.
04

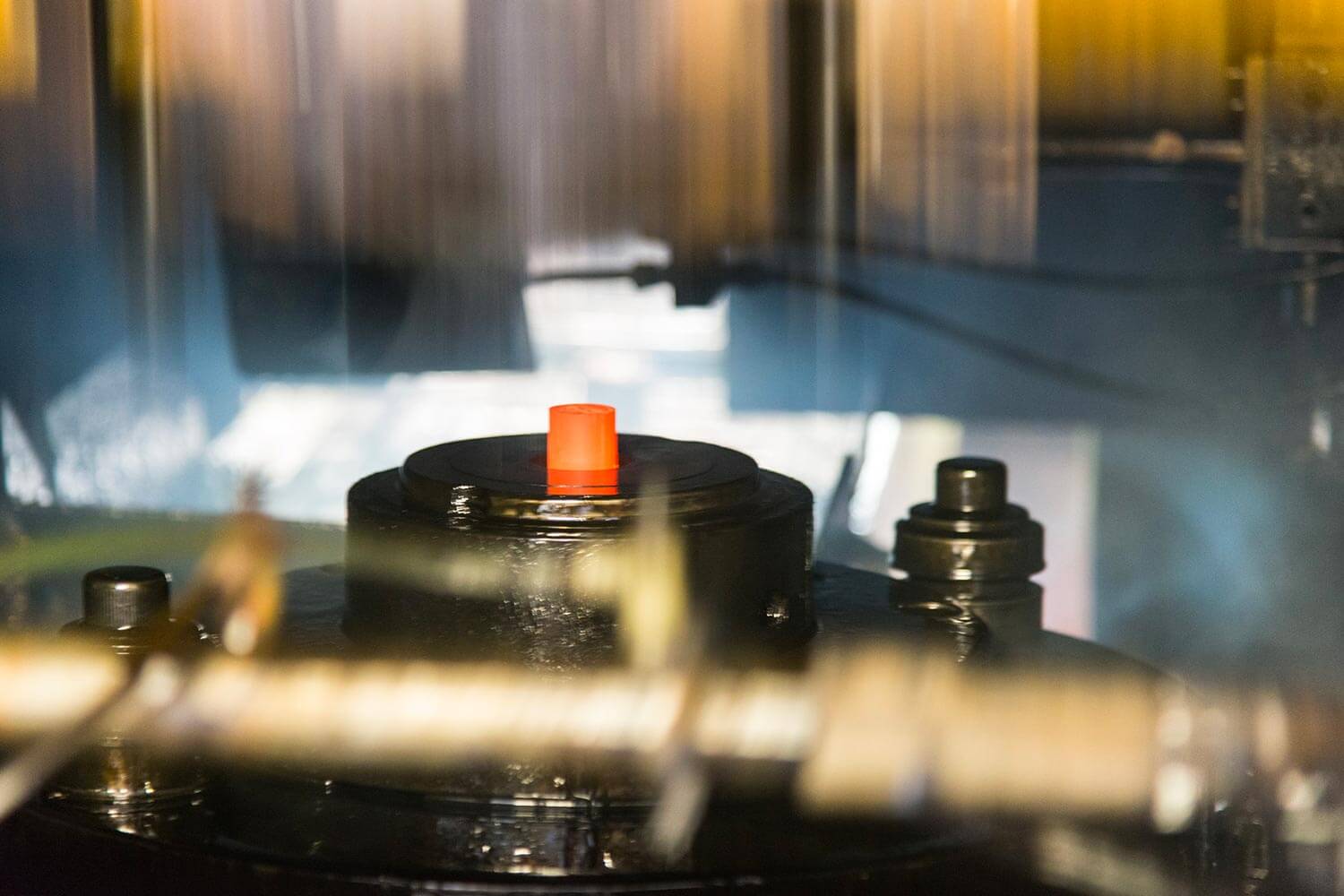
05
05.Quality Control at Every Stage
- Following each machining process, parts undergo a strict inspection using a variety of high-precision measuring instruments.
- This includes profile projectors, micrometers, vernier calipers, and specialized gauges to guarantee all dimensional tolerances are met.
06.Plating Process (if applicable)
- Components requiring a specific surface treatment or plating are sent to the plating department.
- Here, we employ electroplating processes such as PVD, chromium, nickel, copper, or zinc plating to enhance the part's properties.
06

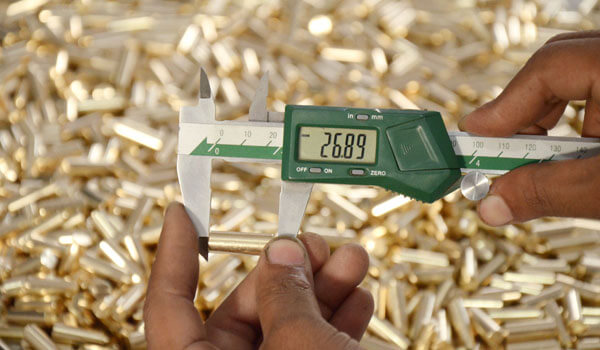
07
07.Final Inspection
- After any surface treatment is completed, the parts undergo a final inspection.
- This inspection may involve tests like salt spray testing to assess corrosion resistance or verification of plating thickness to ensure adherence to specifications.
08.Packaging and Labeling
- Once all inspections are passed, the parts are meticulously packaged and labeled.
- We utilize various packaging materials like sealed poly bags, small boxes, blister packs, or custom kits to suit your needs.
- Labeling is done according to your specific requirements, and the finished goods are palletized based on weight and box volume for safe and secure transportation.
08
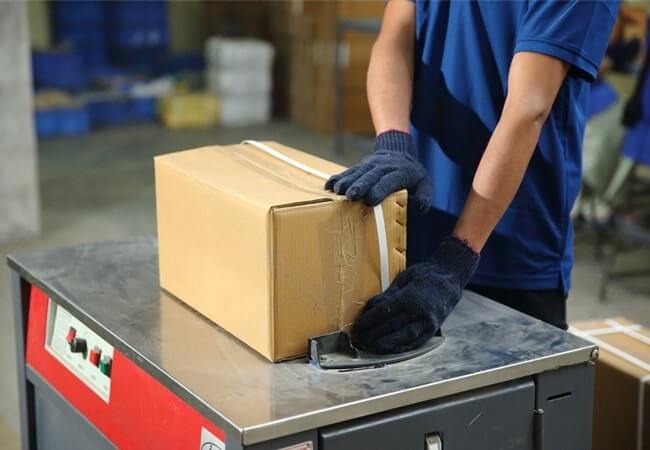
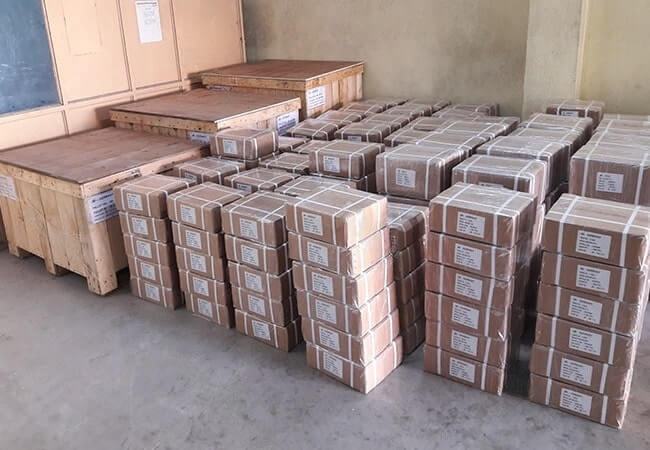
09
09.Dispatch or Storage
- Following packaging and labeling, the components are readied for dispatch or storage
- We maintain a well-organized storage facility to ensure your parts are readily available when needed.
- This comprehensive overview demonstrates our commitment to quality and precision in every step of the brass component manufacturing process. By adhering to these rigorous procedures, we consistently deliver exceptional products that meet your exact requirements.
Celebrating 26+ Glorious years
Modern Technology Infrastructure
Customer Centric Approach
Get in touch
Your search for a reliable Brass Parts Manufacturer ends here. Send us your Requirements now.